Designing for Transit is Essential
The packaging world continues to face new challenges as both society and retail evolve. One such challenge facing packaging designers is the task of quantifying a package‘s ability to protect a product from a myriad of consumer delivery mechanisms. This becomes especially challenging when existing packaging configurations are re-purposed for new supply chains. To help ensure success, it is important for designers to contrast supply chain hazards to product vulnerabilities. As an example, orientation is not guaranteed in a single parcel delivery system (UPS, USPS, FedEx, SF Express, etc.) increasing the likelihood that a liquid product will leak during shipment if it was designed with only vertical orientation in mind. Anticipating these hazards early in the product-package design cycle will enable better packaging optimization across distribution channels. Furthermore, optimizing a packaged-product doesn‘t have to be limited to the packaging, and in some instances, optimizing the product could yield the greatest benefits.
Design tools, such as pre-shipment distribution testing, help confirm insights and offer a valuable understanding of packaged-product performance. Whether bought on a store shelf, fulfilled through an ecommerce retailer, or shipped directly from a product manufacturer, gaining insight into supply chain hazards and ensuring the most appropriate design tool is leveraged are critical to success.
How Testing Helps
The need for testing comes from the difficulty of predicting what will happen in large-scale operations, coupled with the requirement to make decisions prior to implementation. Essentially, every test comes from the need to make a decision. The test results provide the decision-maker with information to help maximize correct decisions. The decisions supported by preshipment performance testing of transport packaging are typically about how well the package will protect the contents during distribution. Testing can also be a mandated activity as part of a package development, new product release, or engineering modification. This testing may be driven by organizational policy (corporate specification, for example), by regulatory application (testing of packaging for hazardous materials and dangerous goods, for example), or by customer requirements (purchase specification, for example). While these situations usually have little flexibility in test selection, they are still in the broad category of supporting decisions on packaging suitability.
The decisions supported by preshipment performance testing of transport packaging are typically about how well the package will protect the contents during distribution.
ISTA's Role
The International Safe Transit Association (ISTA) is a global alliance of shippers, carriers, suppliers, testing laboratories, and educational and research institutions focused on the specific concerns of transport packaging. Our mission is to empower organizations and their people to minimize product damage throughout distribution and optimize resource usage through effective package design.
We help our members control costs, damage, and resources during the distribution of packaged-products by:
- Creating and publishing laboratory preshipment Testing Procedures using our ANSI accredited consensus standards development process.
- Certifying Packaging Laboratories.
- Certifying Packaging Dynamics Professionals (PDP).
- Providing Third-Party verification of testing.
- Offering education, training, and support.
Consensus Body Approach
We're an ANSI Accredited Standards Developer. Since 2014, ISTA has been recognized by the American National Standards Institute’s (ANSI) Executive Standards Council (ExSC) as an ANSI Accredited Standards Developer under its proposed operating procedures for documenting consensus on ISTA-sponsored American National Standards. Being accredited by ANSI as a standards developing organization further validates ISTA as the industry leader in the development of pre-shipment performance testing protocols for packaged products.
The American National Standards Institute (ANSI) coordinates, facilitates, and promotes the development of voluntary consensus standards that are relied upon by industry, government agencies, and consumers across the United States and around the world. ANSI fosters the U.S. standardization system by accrediting the procedures of standard-setting organizations and subsequently approving individual documents as American National Standards (ANS). In order to maintain ANSI accreditation, standards developers must adhere to the ANSI Essential Requirements that govern the consensus development process of American National Standards. All interested and affected parties can participate in a standard's development, as standards developers accredited by ANSI must meet the requirements for openness, balance, consensus and other due process safeguards, according to ANSI.
In 2020, ISTA successfully passed the first routine audit required by ANSI’s Essential Requirements to maintain ANSI accreditation.
Selecting & Using ISTA Test Procedures
An important step in the selection and use of ISTA Procedures and Projects is the user’s familiarity with the actual distribution environment for the packaged products under test. Understanding the flow of packages, how they are shipped and handled and stored, is critical to test selection and results interpretation. Users should regularly observe package distribution, both in the manufacturer’s facility and in warehouses, transportation facilities, vehicles and customer locations. In some cases, users may use measurement instruments and techniques to determine vibration, drop, compression, and temperature/humidity levels during distribution. This detailed knowledge, observation, or measurement may be very useful in test selection, for example, the use of an individual package test protocol instead of or in addition to a unitized load test protocol when loads are broken down during distribution.
Test Considerations
An important consideration in the selection of a test protocol is the objective of running the test, i.e., what information is needed to make the decision associated with this test. Broadly put, these specific objectives for each test might be categorized simply as screening or prediction.
A screening test would be used to avoid serious problems in shipment, usually damage to the product. This test objective category is a common one, and can adequately fill the needs of many users. Screening tests give the user confidence that the chances of serious transport damage have been minimized and have the following general characteristics:
- simple and inexpensive to perform
- widely available and accepted
- utilize simple equipment
- accommodate known and suspected severe hazards
- are not necessarily a simulation of the hazards of distribution
- achieve damage resistance by challenging the strength and robustness of the product and package (a strong product/package resists damage).
Prediction is a more difficult expectation for a preshipment performance test. While screening seeks to avoid serious problems, prediction must allow the user to foresee more subtle effects, such as minor damage, occasional damage, or non-functional problems with the package. In an ideal prediction situation, the tested samples and representative samples of distributed products would be indistinguishable. This is not always entirely possible given the technology mix available today, but it is approachable.
Prediction allows the user to fine-tune cost and environmental impact as well as helping to avoid damage of all types. By testing incrementally reduced cost and material-content designs, the near-optimum configuration could be achieved. Prediction might also allow the user to design a package for a repeatable low level of damage, consistent with an objective of lowest overall system cost. Without a good prediction test to represent field performance, this trade-off of package cost and damage cost would be largely guesswork.
Reminders for Use of ISTA Test Protocols
- Use care in selecting the right test for the situation. In some cases, more than one test should be run and results compared. Field testing (trial shipments) may be used as an adjunct to lab testing.
- Use the current test. ISTA® Projects and Procedures are continuously reviewed, updated and expanded. Keep up to date with changes by checking the ISTA website.
- Use representative samples. Both products and packages should be as close as possible to actual production items. In some cases this may mean testing a product and package early in the development cycle and then later when production products are available. Samples should not have been previously tested, or shipped to a test lab without over-packaging or other consideration.
- Review the test before performing it. Check for new sections, order of tests, documentation requirements.
- Damage/Degradation determination. Most ISTA protocols call for determining the Product Damage Tolerance and Package Degradation Allowance before the test begins.
- Check lab status. If the package is to be Certified by ISTA, the performing lab must have a current laboratory certification, renewable every two years.
- Perform all tests, at the correct levels and in the correct order. ISTA® Procedures and Projects do not allow test levels, times, etc. below the stated values, flexibility in the order of performance, nor the limitation of any tests. Overtests are permitted if desired such as more or higher drops were conducted, the vibration test was run longer or at a higher level, the compression force used was greater, etc. If the purpose of a test does not include ISTA, then ISTA has no official involvement or responsibility and therefore the test can be modified at the user’s discretion. In such situations it is not necessary or desirable to send a Test Report to ISTA.
- Document results as tests are performed. Record intermediate results, options selected, calculations made and any deviations. Photo, video and drawings are good documentation tools.
- Do not alter package condition. Interior inspection of the product or package (by opening the package) is not allowed during the conduct of an ISTA Test Procedure where packaged-product certification is desired. Doing so may alter the package condition and thereby invalidate the test results. If intermediate inspection is desired, the recommended approach is to perform separate tests for investigation and certification. First test one or more packaged-products, inspecting them as desired to determine intermediate damage. When any issues or problems have been corrected, separately subject one or more new packaged-products to the complete test, without intermediate inspections, to determine pass/fail or for certification.
- Determine results. Most procedures require a pass/fail determination. This determination must be made in light of the package and product damage/degradation criteria determined before the test began. Details on how the evaluation was made should be included in the test documentation.
- Review the test. Was it the right test? Was it done correctly? Is the documentation complete? Would you understand it and be able to reproduce it two years from now?
- Finalize. Distribute documentation. Make decisions.
- Monitor Actual Shipments. If possible, obtain information on performance in actual distribution of the packaged-product tested. This performance, when compared to results from the laboratory tests, can be used to evaluate the effectiveness of tests and guide future testing decisions.
Distribution Type | Package Type | ||
---|---|---|---|
150 lbs. (68 kg) or Less | Over 150 lbs. (68 kg) | Pallet Load | |
Parcel Delivery | 3A | Not Applicable | Not Applicable |
LTL (Less-Than-Truckload) Delivery | 3B | 3B | 3B |
Manufacturing to Distribution Center | Not Applicable | Not Applicable | 3E |
Distribution Center to Retail | 3F | Not Applicable | Not Applicable |
eCommerce shipments fulfilled by retailer | 3L, 6-Amazon.com-Over Boxing, 6-Amazon.com-SIOC | 3L, 6-Amazon.com-SIOC | 3L, 6-Amazon.com-SIOC |
eCommerce shipments direct from manufacturer to consumer | 3A | 3B | 3B |
Club Store | 6-Sams Club | 6-Sams Club | 6-Sams Club |
European Consumer Goods | 3K | Not Applicable | Not Applicable |
Specialized Furniture | 2C | 2C | 2C |
Thermal Testing | 7D, 7E | 7D, 7E | Situational |
Bulk/Automotive Reusable | Not Applicable | Not Applicable | 3H |
Custom Test Building | PackSight | PackSight | PackSight |
Preliminary Design Screening Test | 1A, 1C, 1G | 1B, 1D, 1H | 1E |
Partial Simulation | 2A | 2B | Not Applicable |
Retesting
ISTA test protocols should be repeated periodically or as necessary to maintain the quality characteristics of the packaged product on arrival. In addition, tests must be repeated whenever there is a change in the product, the package, or the process. When there is any doubt as to whether a change will potentially affect performance, retesting should be done. Determining when retesting is required may involve knowing and tracking specification details of both the package and the product, such as new or changed components, materials, interior packaging, closure methods, etc.
Transit-Tested Program
To ensure successful launch of any new product, it is imperative to examine all phases of the products life cycle. This includes an evaluation of the packaged-product system to understand its ability to overcome hazards experienced in the supply chain. During the design and development process the full packaged-product system should be evaluated to ensure the desired outcomes such as brand image and sustainability targets are achieved. While there are many ways to evaluate a packaged-product, there are industry best practices that should be leveraged. It was with this intent that ISTA developed the Transit-Tested Program.
Validating a packaged-product using industry best practices creates a process that ensures you are gaining the greatest understanding of performance and reduces the risk of product damage. The industry best practices include:
- testing to the most current version of a general simulation test,
- documenting the results thoroughly including adding pictures,
- testing every variant and limit the amount of bridging knowledge gaps,
- conduct all the test sequences in the correct order at the appropriate intensity level
Transit-Tested Mark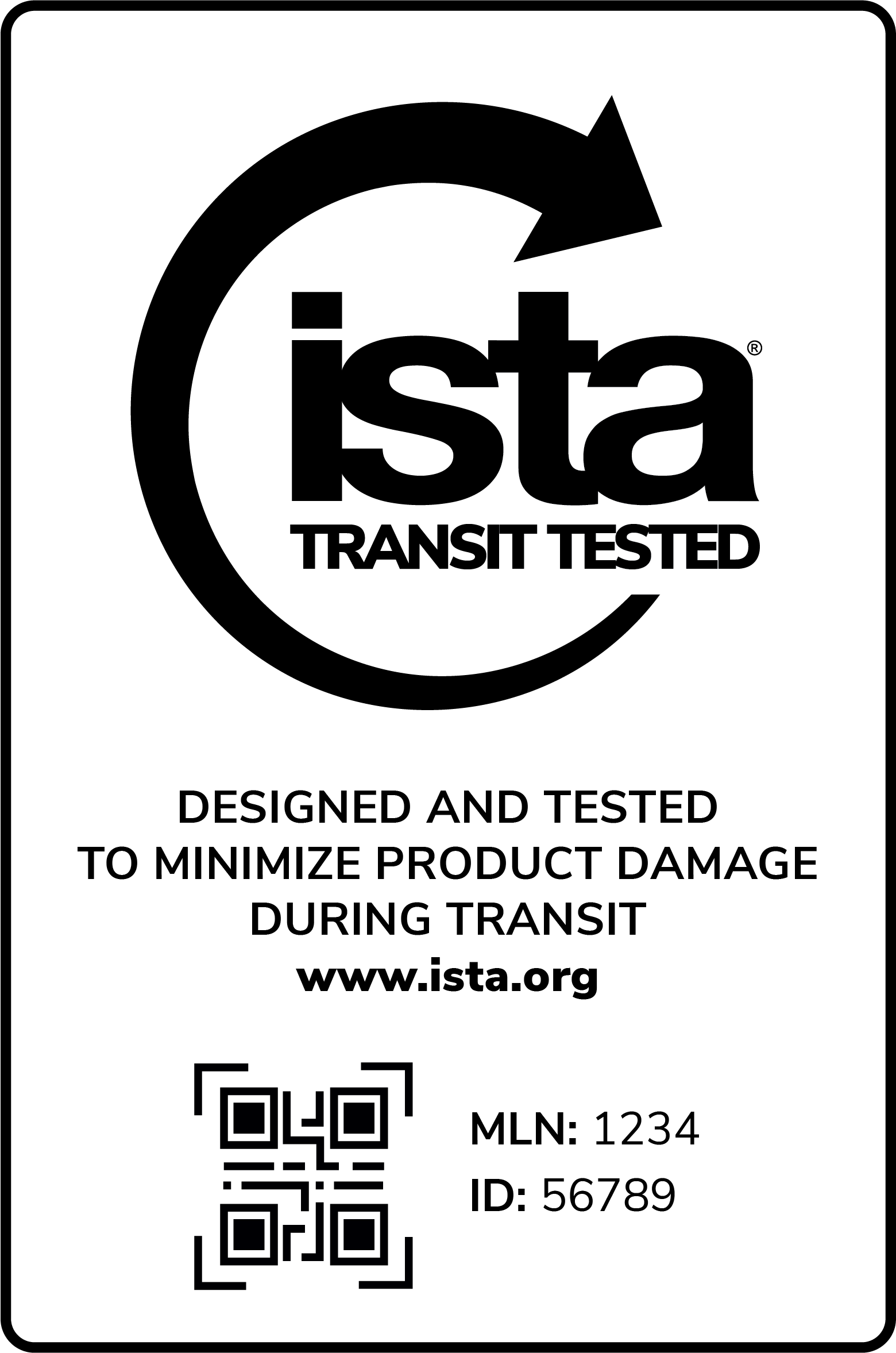
The ISTA Transit -Tested Mark is only available to Shipper members with a signed manufacturer's license agreement (MLN) on file with ISTA. It is visible proof to carriers and customers alike that you have done the diligence of minimizing product damage throughout distribution. Credibility is achieved by successful completion of industry accepted general simulation pre-shipment laboratory tests and having the results reviewed by the test developer. The confidence you gain from these metrics ensures you have the most effective package design for your product’s intended distribution channel. Here is an example of the new ISTA Transit-Tested Mark.
Elevate your brand and drive greater consumer awareness to the diligence done of minimizing product damage during transit by displaying the Transit Tested logo on your packaging.
New test report delivery method: The Transit Test Portal enables Shipper members and Labs, on behalf of the Shipper member, to submit reports for review by ISTA through the Transit Tested Portal. The portal also provides users visibility of all reports submitted for easy future reference.
Find an ISTA Certified Lab & Packaging Services
Locate a testing laboratory capable of performing the testing you require or find companies to help you with package design, test equipment, packaging supplies.
Find nowPackSight
Making package testing easier for you and your team! PackSight, a new online test planning and reporting platform for ISTA test procedures. Simply select a test procedure, enter your test package's weight and dimensions, and PackSight provides a streamlined, step-by-step workflow specific to the test item. You can use a computer or mobile device to collect testing in real-time or print off the workflow. Once testing is complete, reports are auto-generated and stored in a secure cloud environment, making results accessible anywhere, anytime.
Learn more about PackSightResource Book
ISTA's Resource Book includes a collection of the following ISTA Test Procedures and Projects: 1 Series, 2 Series, 3 Series, 7D and the Guidelines for Selecting and Using ISTA Test Procedures. Available in two formats: PDF and Printed & Bound.
Library
The ISTA library contains hundreds of papers, presentations, case studies, white papers and recorded webinars from the best minds in the industry. It is your resource and is a wealth of knowledge and information for anyone involved in transport packaging. Members receive free access to most items. Not an ISTA member? Join ISTA today!
Get Involved!
You can get involved and make a difference! We have several volunteer groups currently leading ISTA in becoming the leading inspiration and resource for improving our world through transport packaging globally. Click below to explore our Boards, Council, Committees or Workgroups and get involved!
Get involved and make an impact