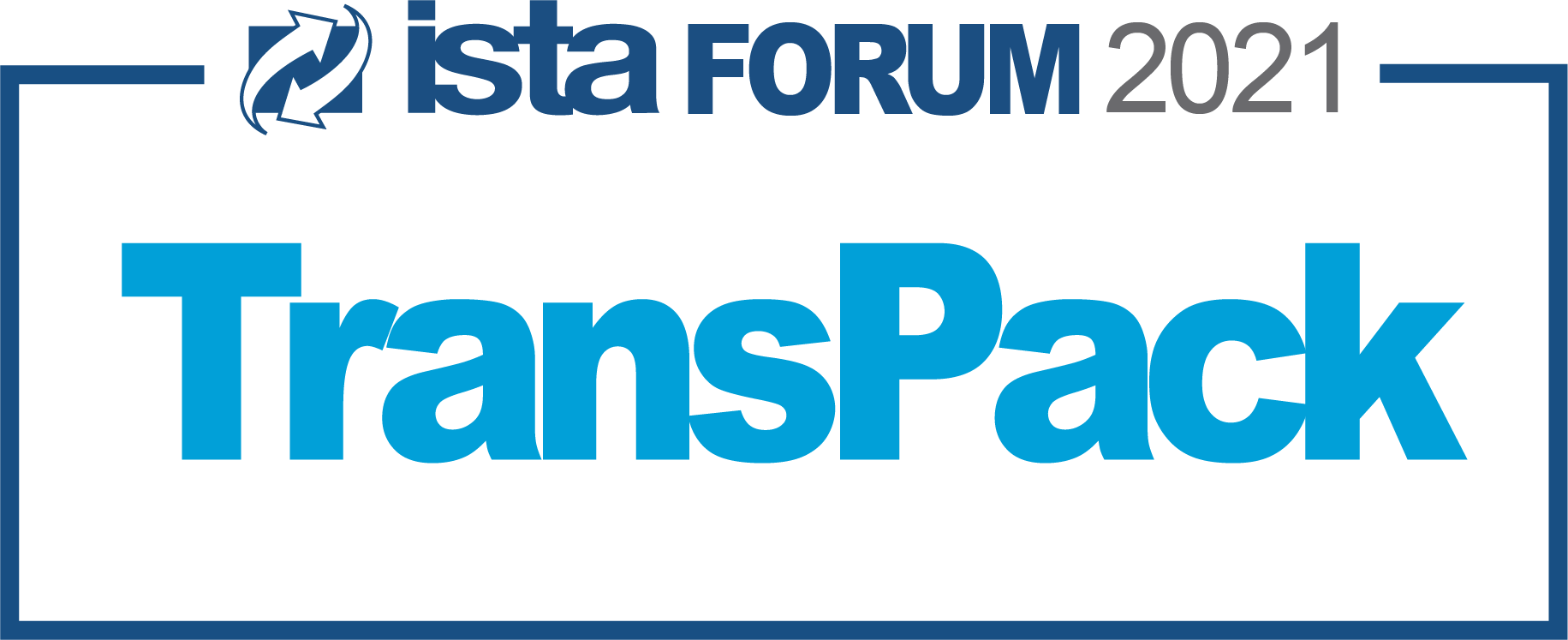

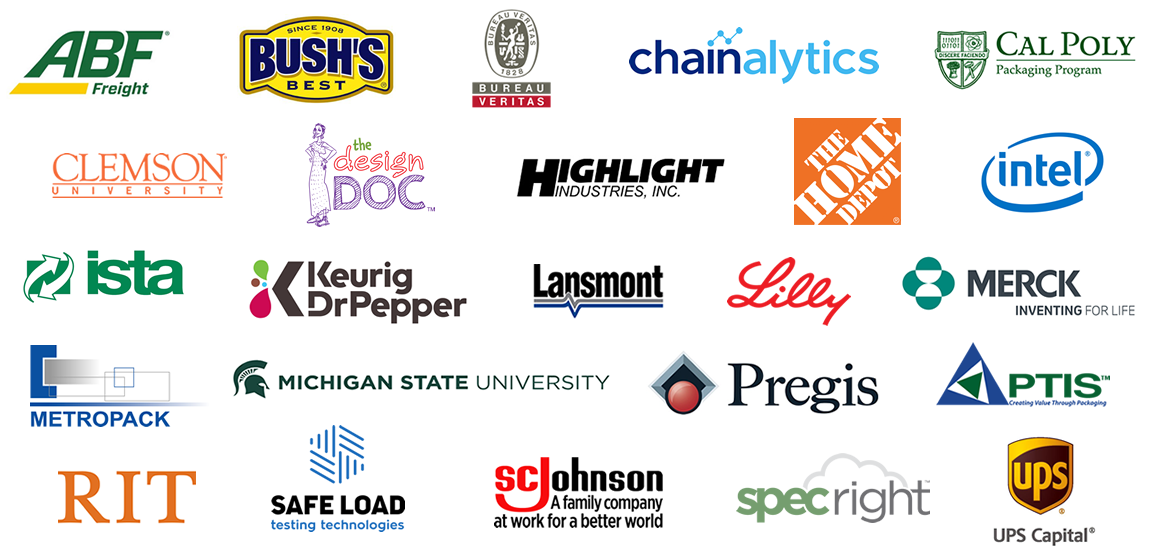

Assistant Professor
Department of Packaging Science College of Engineering Technology
Rochester Institute of Technology
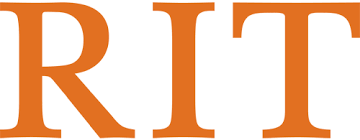
Vibration testing 'under load' is a common test block outlined by many ISTA test procedures to evaluate a container's ability to withstand dynamic compression. To perform this type of vibration test, ISTA recommends the construction of a top-load (TL) apparatus. While ISTA defines the construction parameters of the TL apparatus, many packaging test laboratories have designed alternative systems. Through a laboratory survey, this project aimed to understand the different techniques utilized by current test labs. Based on survey results, the most common TL apparatuses were replicated. Test results will indicate which of the TL apparatuses are best suited for performing vibration with top-load. Additionally, results will be compared to field-collected measurements to understand which TL apparatus most closely resembles compressive forces observed during transport through the small parcel distribution environment.
Takeaways:
- Evaluation of TL apparatus used for ISTA testing
- Understand compressive forces in e-commerce
Actionable Takeaways:
- TL apparatus designs
- Survey results of different TL apparatus
- Understanding of which TL apparatus design best resembles field measured forces
Biography: Education: B.S. and M.S. Packaging Science, Ph.D. Food Technology, Clemson University. Professional Activities: ISTA, ASTM, IFT. Achievements: CPLP - Professional.
The Effect of Temperature and Relative Humidity on Triboelectric Energy Generator Performance

Graduate Research Assistant
Clemson University
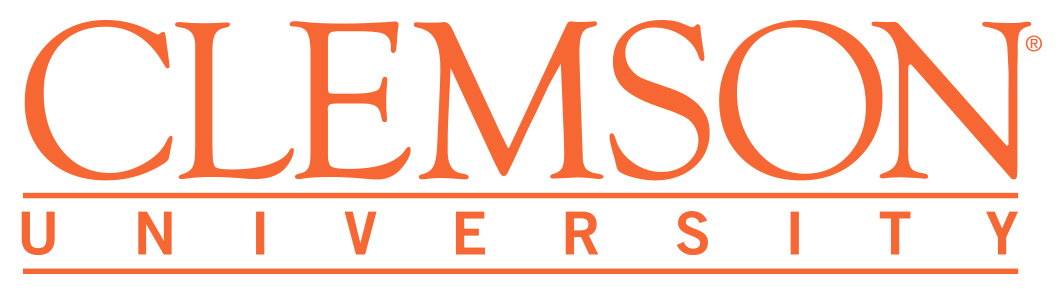
The amount of various forms of data created globally is increasing yearly. One source predicts that data creation will grow to 163 zettabytes by 2025 which is ten times the amount created in 2017 [1]. While this represents a global trend, it also includes data collected in the characterization and monitoring of the distribution environment using various types of sensors like GPS trackers, accelerometers, thermocouples, etc. One thing all these sensors have in common is their need for power. There are various devices used to generate power from mechanical motion as is present throughout packaged product transport. Triboelectric generators are one such low power mechanism that due to their low cost has potential in packaging applications. One company, DTS (Seal Beach, CA), is working on six degree-of-freedom motion recorders that require as little as 0.24mA at 1.4V during recording. A previous study explores the use of triboelectric energy generators in a packaging application in the form of a pallet tier sheet [2]. In this study, the researchers consider a triboelectric energy generator configured as a tier sheet, and its ability to generate enough energy to power sensors like temperature, humidity, and pressure loggers. In the distribution environment, packaged products are exposed to a wide range of temperatures and relative humidities. The research discussed in this presentation focuses on the power generating performance of a triboelectric generator as it is exposed to varying temperatures and relative humidities. In order to perform this research, we mount an optimized triboelectric generator to an electrodynamic shaker located inside an environmental chamber. The set up allows us to replicate various vibration inputs over a wide range of environmental conditions.
References:
1- Paulsen, J. (2019, April 20). Enormous Growth in Data is Coming - How to Prepare for It, and Prosper From It. Retrieved November 9, 2019, from https://blog.seagate.com/business/enormous-growth-in-data-is-coming-how-to-prepare-for-it-and-prosper-from-it/.
2- Barry, A. (2016). The Application of a Triboelectric Energy Harvester in the Packaged Product Vibration Environment (Master’s thesis). Clemson University, South Carolina, USA
Takeaways:
- Further development of the concept triboelectric energy harvesting can be used in a packaging application to power various sensors.
- How temperature and relative humidity effects the performance of triboelectric energy generators
Biography: Master of Science in Packaging Science (Clemson University 2020); Bachelor of Science in Packaging Science with a minor in Business Administration (Clemson University 2018); Graduate research in Environment Effects on the Performance of Triboelectric Energy Generators; Graduate Teaching Assistant for Packaging Dynamics Lab; Undergraduate Packaging Engineer Co-op at Campbell Soup Company; CPLP Technician certification.
Consumer Perceptions of Parcel Packaging
Ryan Germann
Director of Strategy
Pregis
Mike Briestansky
Southeast Regional Sales Manager
Pregis Protective Products
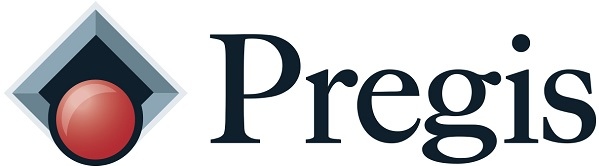
Wonder how consumers' react to the protective packaging decisions we make? This session will explore data from a handful of recent studies to help us better understand the relationship between packaging and the unboxing phenomenon. Topics include; excessive packaging, sustainability, price expectations, and emotions related to unboxing.
Takeaways:
Ryan Germann Biography: Ryan Germann is the Director of Strategy, Market Segmentation for Pregis. In this role, he develops strategies for companies to reduce damages and fulfillment costs while improving customer experience and protecting customer lifetime value through protective packaging solutions. Prior to his five years at Pregis, he spent four years with the logistics leader, FedEx. His combined knowledge of logistics and innovation through packaging is a powerful resource for businesses looking to improve their bottom line.
Mike Briestansky Biography: Mike has 10+ years of experience in the packaging industry. He has seen firsthand how end user buying motives have been changing across many industry segments over that time. The shift has seen protective packaging decisions expand across departments and escalate to higher levels within organizations. Mike’s combination of packaging expertise, market trends, and customer focus has made him a powerful resource for businesses looking to maximize the value packaging can provide.
The Impact of Packaging on Cargo Insurance
Amir Ghoddousi
Director of Sales
UPS Capital
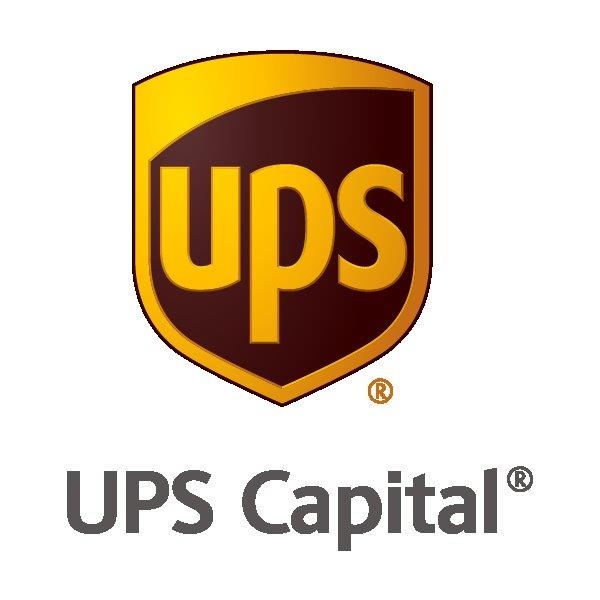
Unpredictable events like damage, loss and delay can be devastating to a brand’s reputation, not to mention their bottom line. Self-insuring or relying on carrier liability leaves significant gaps in coverage, making companies susceptible to glitches in their supply chain. Throughout this discussion we will explore the existing risks in the logistics industry, how a comprehensive insurance solution can alleviate these risks and ultimately how sufficient packaging is key to a successful supply chain.
ISTA Technical Update
Eric Hiser
Vice President of Technical
ISTA
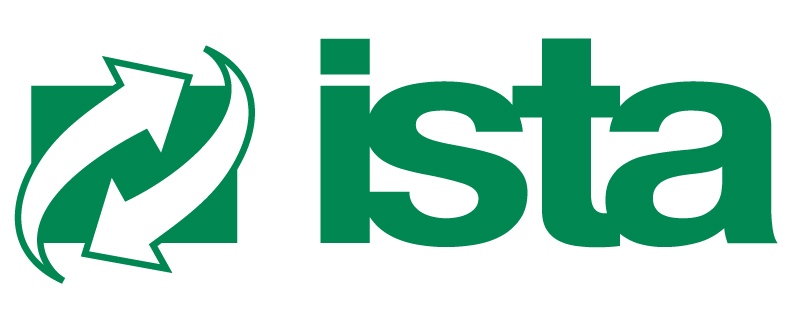
Get an update on what is happening within ISTA’s technical community including new test development, protocol changes, enhancements to the lab certification process, and more.
Eric Hiser Biography: Eric Hiser is Vice President of Technical Operations at International Safe Transit Association (ISTA). He manages the ISTA Technical Division including all technical activities, development and maintenance of ISTA Procedures and Projects, and ISTA Certification programs for labs, packaged-products and people.Eric is a graduate of the Michigan State University School of Packaging with a Bachelor of Science Degree in Packaging. He is an IoPP Certified Packaging Professional (CPP) and has an extensive background in transport packaging performance testing as well as developing packaging for the Consumer Packaged Goods (CPG) market.He stays involved in the packaging community through participation on industry groups such as IoPP transport packaging and medical device committees as well as serves on the industrial advisory board for Packaging Science at RIT.
Eric Hiser
Vice President of Technical
ISTA
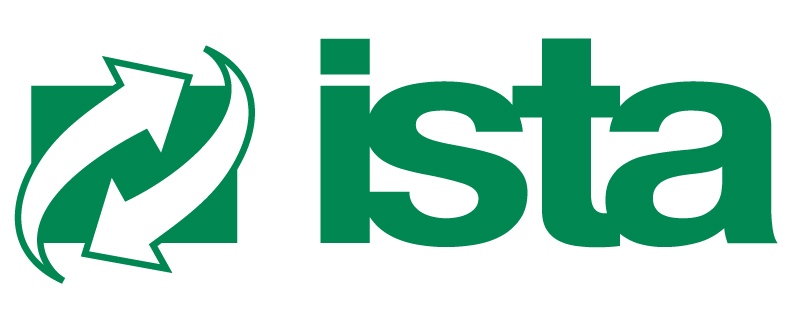
Matthew Wright
Founder & CEO
Specright
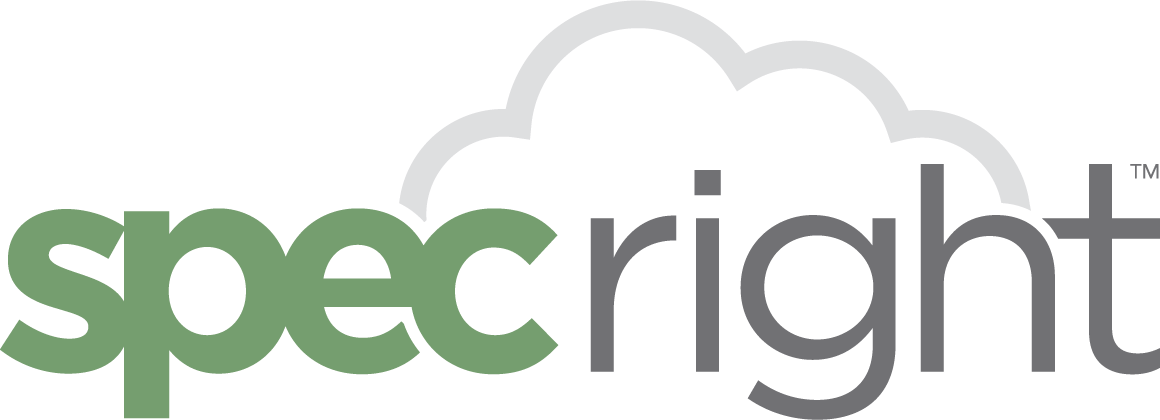
Learn more about how PackSight, ISTA’s new online test planning and reporting platform for ISTA test procedures is transforming the way packaging testing is performed. PackSight, powered by Specright is a secure, cloud-based, global, mobile, and web access workflow tool with a central data repository for ISTA testing. Labs can now select, collect and analyze autogenerated test reports within PackSight, creating efficiencies and visibility for stakeholders across the supply chain.
Eric Hiser Biography: Eric Hiser is Vice President of Technical Operations at International Safe Transit Association (ISTA). He manages the ISTA Technical Division including all technical activities, development and maintenance of ISTA Procedures and Projects, and ISTA Certification programs for labs, packaged-products and people.Eric is a graduate of the Michigan State University School of Packaging with a Bachelor of Science Degree in Packaging. He is an IoPP Certified Packaging Professional (CPP) and has an extensive background in transport packaging performance testing as well as developing packaging for the Consumer Packaged Goods (CPG) market.He stays involved in the packaging community through participation on industry groups such as IoPP transport packaging and medical device committees as well as serves on the industrial advisory board for Packaging Science at RIT.
Matthew Wright Biography: Matthew Wright is the Founder & CEO of Specright and has spent over 25 years in the packaging industry. Prior to founding Specright, he held leadership positions at International Paper, Temple Inland, and rightPAQ — a packaging company he co-founded. He has also been involved in leading multiple M&A deals in the packaging industry. He sits on the Packaging Advisory Board at Cal-Poly San Luis Obispo.
Correlation between ISTA Vibrations Protocols Spectrums and European Trucks?
Victor Huart
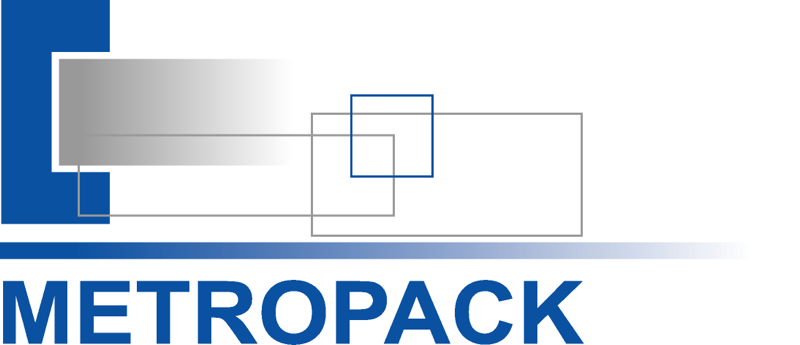
The determination of ISTA trucks vibrations profiles is based on years of stress recording. These constraints are particularly representative of the transport on the American territory. In Europe, the typology and technologies used for road transport are generally different.
As for American trucks, European trucks generate 3 main peaks of vibrations:
Although the general shapes of the spectrums are similar, PSDs recorded on European roads nevertheless show differences in frequency bands of these main vibration peaks.
The purpose of this presentation is to compile thousands of kilometers of road registration in Europe to carry a representative PSD of an European truck.
This representative PSD will be compared to the ISTA vibrations profiles to quantify the difference between a UE spectrum and a US spectrum.
Takeaways:
Consumer Perceptions of Parcel Packaging

Director of Strategy
Pregis

Southeast Regional Sales Manager
Pregis Protective Products
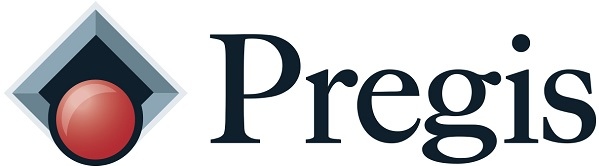
Wonder how consumers' react to the protective packaging decisions we make? This session will explore data from a handful of recent studies to help us better understand the relationship between packaging and the unboxing phenomenon. Topics include; excessive packaging, sustainability, price expectations, and emotions related to unboxing.
Takeaways:
- Unboxing phenomenon introduction/update
- Understand relationship between packaging and consumers in ecommerce
- Research from top universities: Clemson, Cal Poly, Wisconsin
Ryan Germann Biography: Ryan Germann is the Director of Strategy, Market Segmentation for Pregis. In this role, he develops strategies for companies to reduce damages and fulfillment costs while improving customer experience and protecting customer lifetime value through protective packaging solutions. Prior to his five years at Pregis, he spent four years with the logistics leader, FedEx. His combined knowledge of logistics and innovation through packaging is a powerful resource for businesses looking to improve their bottom line.
Mike Briestansky Biography: Mike has 10+ years of experience in the packaging industry. He has seen firsthand how end user buying motives have been changing across many industry segments over that time. The shift has seen protective packaging decisions expand across departments and escalate to higher levels within organizations. Mike’s combination of packaging expertise, market trends, and customer focus has made him a powerful resource for businesses looking to maximize the value packaging can provide.
The Impact of Packaging on Cargo Insurance

Director of Sales
UPS Capital
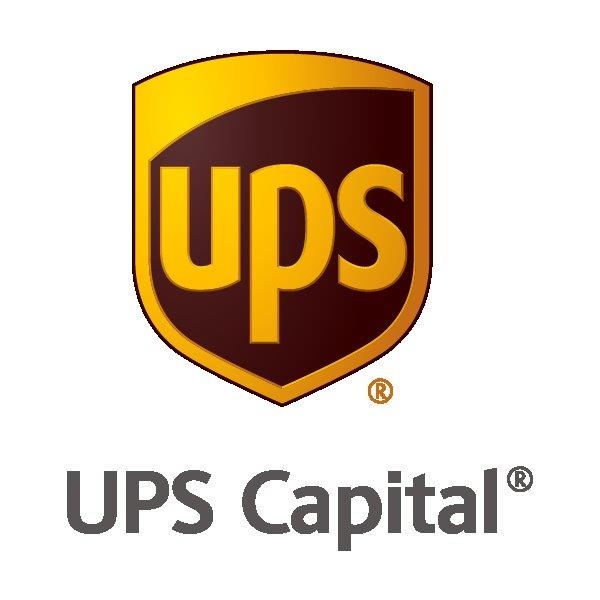
Unpredictable events like damage, loss and delay can be devastating to a brand’s reputation, not to mention their bottom line. Self-insuring or relying on carrier liability leaves significant gaps in coverage, making companies susceptible to glitches in their supply chain. Throughout this discussion we will explore the existing risks in the logistics industry, how a comprehensive insurance solution can alleviate these risks and ultimately how sufficient packaging is key to a successful supply chain.
Biography: Amir Ghoddousi received his B.S. from Michigan State University in Packaging Engineering, and is currently an EMBA Candidate at the University of Notre Dame – Mendoza College of Business. Starting his career at UPS as a Packaging Engineer, Amir has since gained experience in Account Management, Customer Experience, and currently holds the title of Director of Sales at UPS Capital.
ISTA Technical Update

Vice President of Technical
ISTA
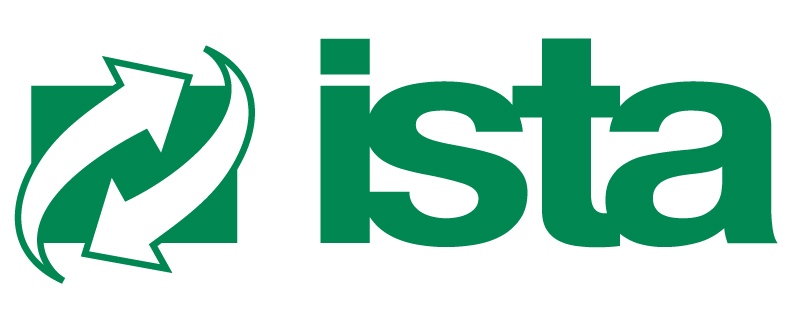
Get an update on what is happening within ISTA’s technical community including new test development, protocol changes, enhancements to the lab certification process, and more.
Eric Hiser Biography: Eric Hiser is Vice President of Technical Operations at International Safe Transit Association (ISTA). He manages the ISTA Technical Division including all technical activities, development and maintenance of ISTA Procedures and Projects, and ISTA Certification programs for labs, packaged-products and people.Eric is a graduate of the Michigan State University School of Packaging with a Bachelor of Science Degree in Packaging. He is an IoPP Certified Packaging Professional (CPP) and has an extensive background in transport packaging performance testing as well as developing packaging for the Consumer Packaged Goods (CPG) market.He stays involved in the packaging community through participation on industry groups such as IoPP transport packaging and medical device committees as well as serves on the industrial advisory board for Packaging Science at RIT.
Introducing PackSight
ISTA’s new online test planning and reporting platform for ISTA test procedures.
ISTA’s new online test planning and reporting platform for ISTA test procedures.

Vice President of Technical
ISTA
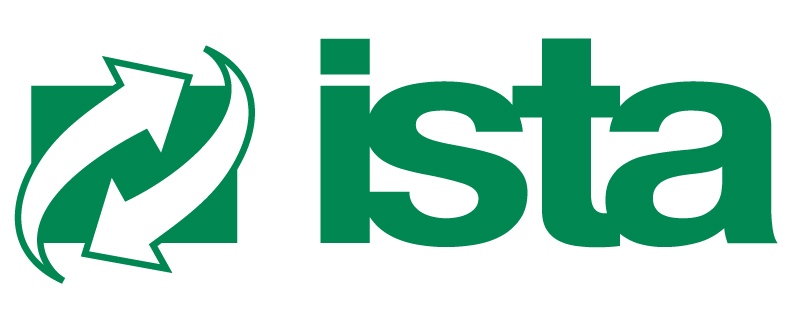

Founder & CEO
Specright
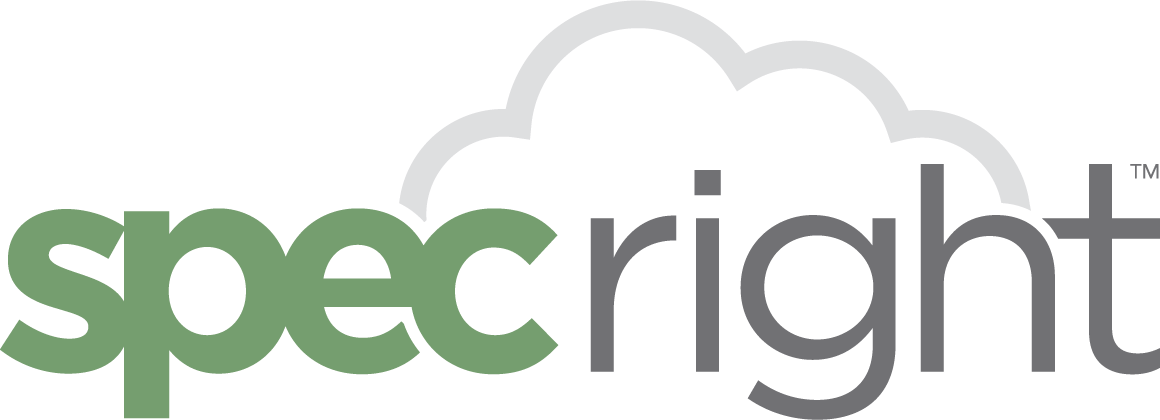
Learn more about how PackSight, ISTA’s new online test planning and reporting platform for ISTA test procedures is transforming the way packaging testing is performed. PackSight, powered by Specright is a secure, cloud-based, global, mobile, and web access workflow tool with a central data repository for ISTA testing. Labs can now select, collect and analyze autogenerated test reports within PackSight, creating efficiencies and visibility for stakeholders across the supply chain.
Eric Hiser Biography: Eric Hiser is Vice President of Technical Operations at International Safe Transit Association (ISTA). He manages the ISTA Technical Division including all technical activities, development and maintenance of ISTA Procedures and Projects, and ISTA Certification programs for labs, packaged-products and people.Eric is a graduate of the Michigan State University School of Packaging with a Bachelor of Science Degree in Packaging. He is an IoPP Certified Packaging Professional (CPP) and has an extensive background in transport packaging performance testing as well as developing packaging for the Consumer Packaged Goods (CPG) market.He stays involved in the packaging community through participation on industry groups such as IoPP transport packaging and medical device committees as well as serves on the industrial advisory board for Packaging Science at RIT.
Matthew Wright Biography: Matthew Wright is the Founder & CEO of Specright and has spent over 25 years in the packaging industry. Prior to founding Specright, he held leadership positions at International Paper, Temple Inland, and rightPAQ — a packaging company he co-founded. He has also been involved in leading multiple M&A deals in the packaging industry. He sits on the Packaging Advisory Board at Cal-Poly San Luis Obispo.
Correlation between ISTA Vibrations Protocols Spectrums and European Trucks?

Research and Development Manager
Metropack
Metropack
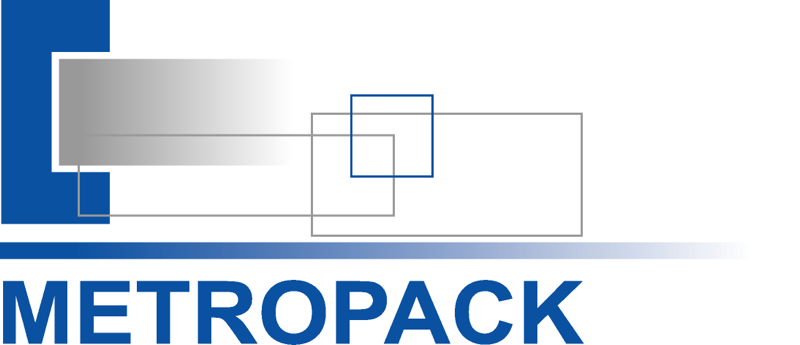
The determination of ISTA trucks vibrations profiles is based on years of stress recording. These constraints are particularly representative of the transport on the American territory. In Europe, the typology and technologies used for road transport are generally different.
As for American trucks, European trucks generate 3 main peaks of vibrations:
- 1 peak for truck dampers ;
- 1 peak for truck tires ;
- 1 peak related to the structure of the truck.
Although the general shapes of the spectrums are similar, PSDs recorded on European roads nevertheless show differences in frequency bands of these main vibration peaks.
The purpose of this presentation is to compile thousands of kilometers of road registration in Europe to carry a representative PSD of an European truck.
This representative PSD will be compared to the ISTA vibrations profiles to quantify the difference between a UE spectrum and a US spectrum.
Takeaways:
- comparison between US and UE trucks vibrations excitations
- proposition of adapted PSD for UE transport
- method of test time reduction
Biography: Victor Huart is a Research and Development Manager at METROPACK in Reims, France. He holds a Packaging Engineering degree of the ESIReims (ESIEC) and a Ph.D on safety and industrial risk of transport. Victor is specialized in the mechanical stress studies and the packaging mechanical behavior during transport. Integrated in 2013 at METROPACK, a laboratory of test and transport simulation on packaging, he investigates the mechanical behavior of packaging and the fatigue phenomena. At METROPACK, his main aim is to develop methods of transport analysis, establish audits of the customers’ supply-chains and their packaging.
E-commerce Package Design for Less-Than-Truckload Delivery

Senior Manager - Packaging Engineering & Material
ABF Freight
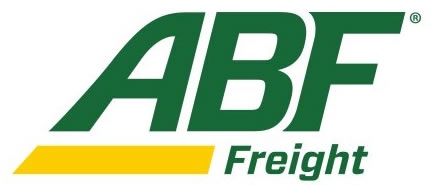
A portion of the ecommerce market requires less-than-truckload delivery and specialized services. This presentation will discuss unique package design needs for the physical, climatic, and assembly challenges of less-than-truckload e-commerce deliveries.
Takeaways: Audience will learn the unique elements of the LTL shipment and delivery including: material handling equipment, entry challenges, stairs, temperature/humidity/moisture/wind, hills, and unpaved surfaces.
Biography: B.S. & M.S. in Packaging, Michigan State University. 25+ years of experience designing packaging for small parcel, truckload, ocean, and LTL distribution. IoPP CPP-Fellow. ISTA CPLP-professional, Technical Council director, Former Chair - Testing Council. Active in ASTM-D10.
Are You Connecting? Or Are You Just Talking?

Engineer Specialist
Bush Brothers & Co.
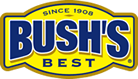
Do you ever get that feeling that you are doing plenty of talking, but nobody is doing plenty of listening? Despite what we may like to think, the problem is usually NOT the listener! For many of us, the issue is us! It's not in our talking, or our content, but the problem is buried in HOW we deliver it! In this 2020 edition of one or Robby's popular talks on making our work more effective, and more rewarding, Robby will help us see key elements that we should consider if we want to be heard more often.
Takeaways: Attendees will learn or be reminded of key aspects of making their words and message land effectively.
Leaders and followers alike will learn about:
- Who do we think this is all about?
- Why getting words right is only the starting place.
- What is required to communicate AND connect effectively.
- Why you must commit to know your audience!
- What it will take for you to ultimately become an effective connector.
Biography: A man who has learned from experience to lead by following, Robby Martin is a husband, father and a really good friend to have in your corner. In the ever-changing world of Packaging & Manufacturing for over thirty years, Robby excels at removing chaos from the process by providing coordination, support and direction to projects ranging from simple manufacturing optimizations to national launches of major brand platforms. Today he supports Bush Brothers & Company with their New Product Innovation efforts as an Engineering Technologist. He specializes in Manufacturing Partner Engagement and New Product Launch Execution. Robby is also a Certified John Maxwell Speaker and Coach. His greatest passion is helping others make their way through the confounding world of personal and professional growth.
Measuring and Observing the Effects of Side Impacts and Low G/Long Duration Events
Patrick McDavid
Instructor
MSU School of Packaging 
Testing events such as horizontal impacts and low G/long duration (vehicle turning, acceleration, and breaking) events with actual unit’s loads is preferred, but they are difficult to instrument. When testing units loads to failure, there are product costs (loss) to account for and there can be messes to clean up. This presentation will discuss early testing of a reusable unit load (S.U.L.I.I. – Simulated Unit Load with Integrated Instrumentation) which could be used to accurately measure field events anywhere in within the unit load for later correlation to lab testing. Proof of concept through its current design will be discussed including field and lab test results as well as future design iterations.
Takeaways: Looking for new ways to gather data and take a closer look at these types of field events. Create opportunities to open up discussion on research and ideas on the future of testing for these events.
Biography: Bachelor’s degree: Packaging (MSU – 1997)). Masters: Supply Chain Management (Elmhurst College - 2008). MBA (Elmhurst College - 2010).
Top Load Equivalency Study
Sean McKillop
Student
MSU School of Packaging 
There are currently multiple ISTA approved methods of testing which can simulate the static compression strength of a box. In this study, the equivalency factor between the “Apply & Release Test” and the “Apply and Hold Test” is being evaluated. The current factor is 1.4. This means that the value used for the hour long “Apply & Hold” method can be multiplied by 1.4 in order to equal the required peak load of the faster “Apply & Release Test”. In previous testing, the value of 1.4 was shown to be too low and may not accurately equate the two test methods. This project will further evaluate the current factor and determine what kind of adjustments may be needed.
Takeaways: The study will be key in providing a more accurate method of testing compression equivalency. By subjecting boxes & shippers to more accurate testing, it can be ensured that they do not fail during transit.
Biography: Senior studying Packaging at Michigan State University. Intern with Haney Packaging Resource Center in Cincinnati, OH. Intern with Ethicon Endo-Surgery, also in Cincinnati. Upon graduation, will begin working full time for Bayer Radiology in Pittsburgh, designing sterile packaging for components of MRI/CT/CV machines.
ISTA Research Update
Brian O’Banion
Vice President of Research & Education
ISTA
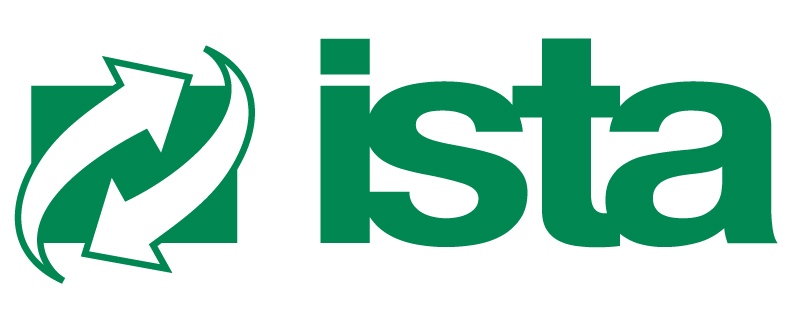
This presentation will be a re-introduction of the ISTA Distribution Environment Data Collection Program, which was presented at the 2019 Forum program. This iteration will include summary results from India and an update on our efforts in the European Union, along with an outreach effort to researchers that may be interested in helping us with data collection in China, Japan and Mexico.
Biography: Brian holds a Master of Administrative Science degree from Johns Hopkins University and a B.S. degree in Chemical Engineering from the University of Michigan. Brian has nearly 20 years of trade association management experience addressing packaging industry issues in a wide variety of areas, including technical, environmental, health, safety, RFID, competing materials, and sustainability. He also has notable experience within the global food and beverage packaging technologies space. As ISTA’s Vice President of Research & Education, Brian plays a critical role in establishing and executing the association’s long-range strategy and vision for research programs and education services.
Measuring and Observing the Effects of Side Impacts and Low G/Long Duration Events

Instructor
MSU School of Packaging

Testing events such as horizontal impacts and low G/long duration (vehicle turning, acceleration, and breaking) events with actual unit’s loads is preferred, but they are difficult to instrument. When testing units loads to failure, there are product costs (loss) to account for and there can be messes to clean up. This presentation will discuss early testing of a reusable unit load (S.U.L.I.I. – Simulated Unit Load with Integrated Instrumentation) which could be used to accurately measure field events anywhere in within the unit load for later correlation to lab testing. Proof of concept through its current design will be discussed including field and lab test results as well as future design iterations.
Takeaways: Looking for new ways to gather data and take a closer look at these types of field events. Create opportunities to open up discussion on research and ideas on the future of testing for these events.
Biography: Bachelor’s degree: Packaging (MSU – 1997)). Masters: Supply Chain Management (Elmhurst College - 2008). MBA (Elmhurst College - 2010).
Top Load Equivalency Study

Student
MSU School of Packaging

There are currently multiple ISTA approved methods of testing which can simulate the static compression strength of a box. In this study, the equivalency factor between the “Apply & Release Test” and the “Apply and Hold Test” is being evaluated. The current factor is 1.4. This means that the value used for the hour long “Apply & Hold” method can be multiplied by 1.4 in order to equal the required peak load of the faster “Apply & Release Test”. In previous testing, the value of 1.4 was shown to be too low and may not accurately equate the two test methods. This project will further evaluate the current factor and determine what kind of adjustments may be needed.
Takeaways: The study will be key in providing a more accurate method of testing compression equivalency. By subjecting boxes & shippers to more accurate testing, it can be ensured that they do not fail during transit.
Biography: Senior studying Packaging at Michigan State University. Intern with Haney Packaging Resource Center in Cincinnati, OH. Intern with Ethicon Endo-Surgery, also in Cincinnati. Upon graduation, will begin working full time for Bayer Radiology in Pittsburgh, designing sterile packaging for components of MRI/CT/CV machines.
ISTA Research Update

Vice President of Research & Education
ISTA
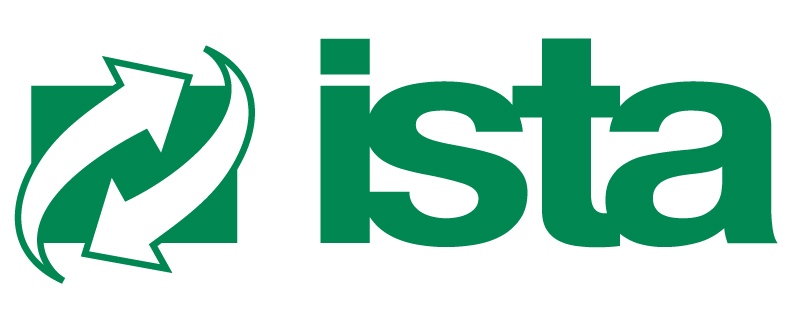
This presentation will be a re-introduction of the ISTA Distribution Environment Data Collection Program, which was presented at the 2019 Forum program. This iteration will include summary results from India and an update on our efforts in the European Union, along with an outreach effort to researchers that may be interested in helping us with data collection in China, Japan and Mexico.
Biography: Brian holds a Master of Administrative Science degree from Johns Hopkins University and a B.S. degree in Chemical Engineering from the University of Michigan. Brian has nearly 20 years of trade association management experience addressing packaging industry issues in a wide variety of areas, including technical, environmental, health, safety, RFID, competing materials, and sustainability. He also has notable experience within the global food and beverage packaging technologies space. As ISTA’s Vice President of Research & Education, Brian plays a critical role in establishing and executing the association’s long-range strategy and vision for research programs and education services.
Intel Corporation's Revolution in Silicon Wafer Transportation

Sr. Packaging Engineer
Intel – ADC
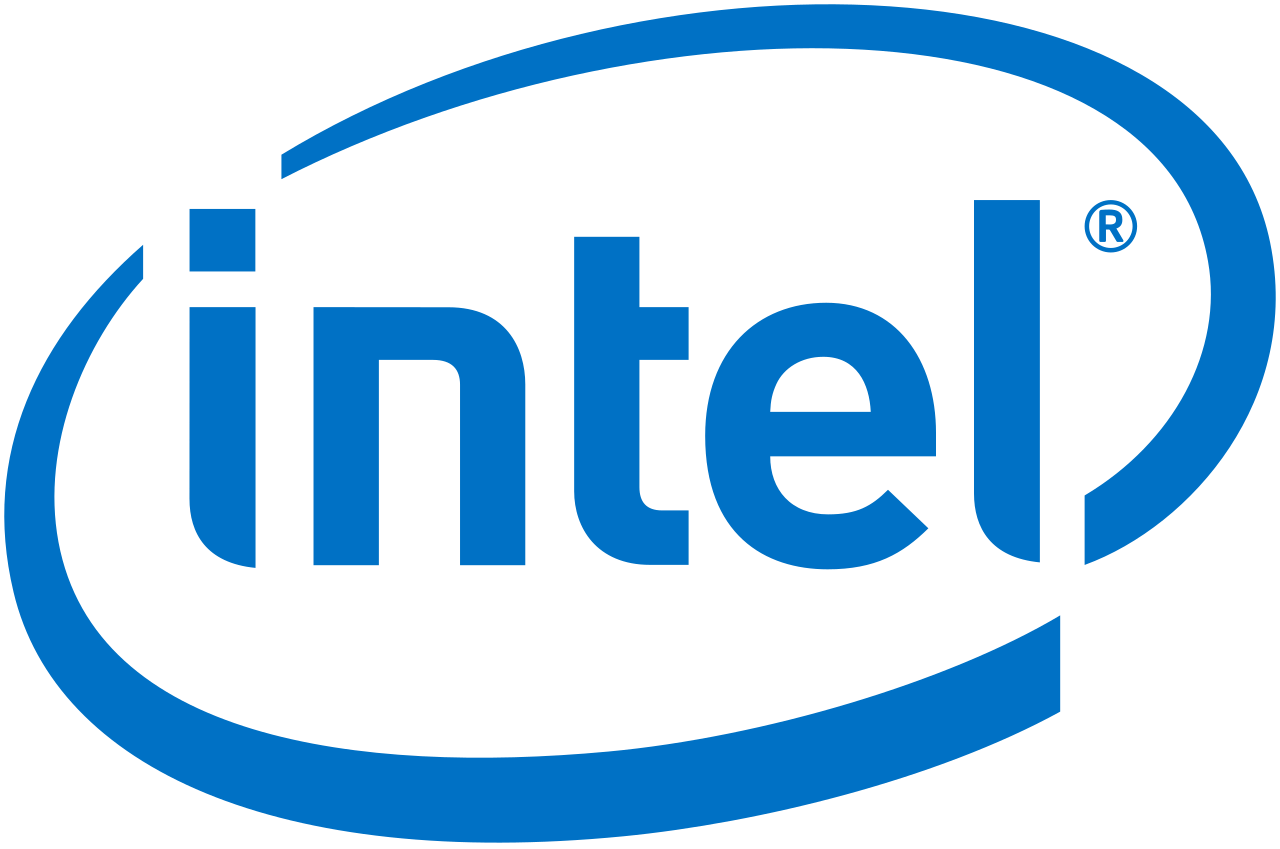
The Horizontal Wafer Shipper (HWS) or coin stack is a low-cost, high-protection media used to ship 300mm silicon wafers as an alternative to the higher-cost, larger Front Opening Shipping Box (FOSB) that had been in use at Intel for 20 yrs. The benefits it provides are: lower freight costs (HWS is 68% smaller than FOSB), lower materials costs (by 60-75%), environmental savings (less fuel and materials consumption), and higher wafer protection.
Objective: Introduce a new wafer media solution to Intel manufacturing sites that provides greater protection with lower overall cost of ownership for Intel. Drive a significant change to Intel's #1 product as handling wafers and ensuring they are delivered without defect is our top priority and something we need to maintain at a world class level.
Process: The HWS cassette and rings went through a supplier selection, multiple designs were evaluated and modified to ensure no defect would occur during loading, unloading or transport of Intel's 300mm wafers. Multiple experiments and pilots were conducted to ensure this change would have no negative impacts. A typical 300mm wafer will break around 45G's in a FOSB, HWS can exceed 500G's before damage occurs.
Our initial package design was changed when we found a ring defect for a short-term solution while modifications were made to the ring. Once the media was improved, we went back to the 70% reduction.
Outcome: We currently have tools installed across the virtual factory, with more tools on order. We've completed multiple WP's and are approved to ship production wafers between Fabrication and Sort and FG Assembly sites today. We improved wafer fragility while in transit 10x, while also reducing particles in comparison to POR, especially for smaller bin (<0.5um). Multiple experiments and pilots have shown no change to product quality at multiple inspection points. We've also found benefit in fab storage by using HWS to free up stocker and FOUP capacity within the site.
Savings: By changing from a polycarbonate FOSB to a smaller HWS/ring made of polypropylene and polycarbonate every lot that ships now uses over 3kg less plastic. With the inherent protection of the HWS we were also able to dramatically reduce our packaging foam materials switching from polyurethane material to an easier to recycle polyethylene which also resulted in over 2kg weight reduction. In total we expect annual reduction of 5.5M KWH (529 avg homes) of energy, 4.3M Liters (27k barrels) of H20 and over 600k KG (100 cars annual) of Co2 from these material changes resulting in significant environmental savings.
This program touches almost every division within Intel's manufacturing division and is expected to deliver Millions of dollars in savings by reducing the chargeable shipping weight when fully deployed. The journey for implementation of HWS has been long and is still in progress on some new technologies, however, the program team has not only driven our suppliers to new levels but helped innovate and create a paradigm shift regarding wafer media handling at Intel.
Takeaways: Intend to share details in media designs and selection process. Packaging solutions to help fix some of the early design fails to allow the project to move forward. Will share investigative testing completed and qualification procedures. Attendees will walk away with possible new trouble shooting techniques and qualification procedures as well as learning about new electronic packaging and medias.
Biography: Ryan is a 2004 Cal Poly, Industrial Technology Grad. Post Cal Poly he started a career at Intel Corporation starting as an Intern to know being one of the longest tenured employees in his group. Ryan was able to use his learn by doing and hands only approach from Cal Poly to successfully make significant contributions at Intel.
How Do I Design a Test if I Don’t Know My Supply Chain?

Principal Packaging COE
SC Johnson
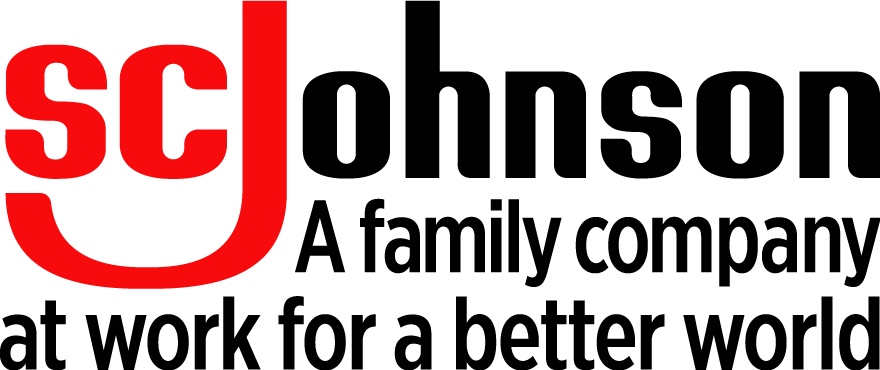
Problem to solve: How do we properly design, test and validate our product to withstand the rigor of distribution within a region and from one region to another region?
Solution: Understand your supply chain handling process and create a test protocol for more robust and faster validation.
Opportunity: Create an intuitive, informative and interactive process map of SC Johnson’s global supply chain environment to assist in product development and validation. Utilize process maps to create regional simulated distribution test protocols. Additionally create a BCT (Box Compression Test) tool and PSF (Product Support Factor) procedure for a corrugate performance-based specification that is supplier agnostic based on the regional supply chain criteria.
Takeaways:
- Understanding your supply chain leads to creating an appropriate distribution test protocol.
- A reference tool that is a quick and easy to understand with enough but not overwhelming detail of the global supply chain which allows users to make the appropriate decisions based on where it is produced to where it is sold.
- Continue to understand your supply chain, your customers supply chains and adjust your protocol based on those learning’s, where applicable.
- Collaborate with industry members to continue research to continually improve the robustness of your protocols.
Navigating Amazon's SIOC Packaging Program: Approach and Best Practices from Keurig Dr Pepper

Packaging Development Engineer III
Keurig Dr Pepper

Packaging Engineering Manager
Keurig Dr Pepper
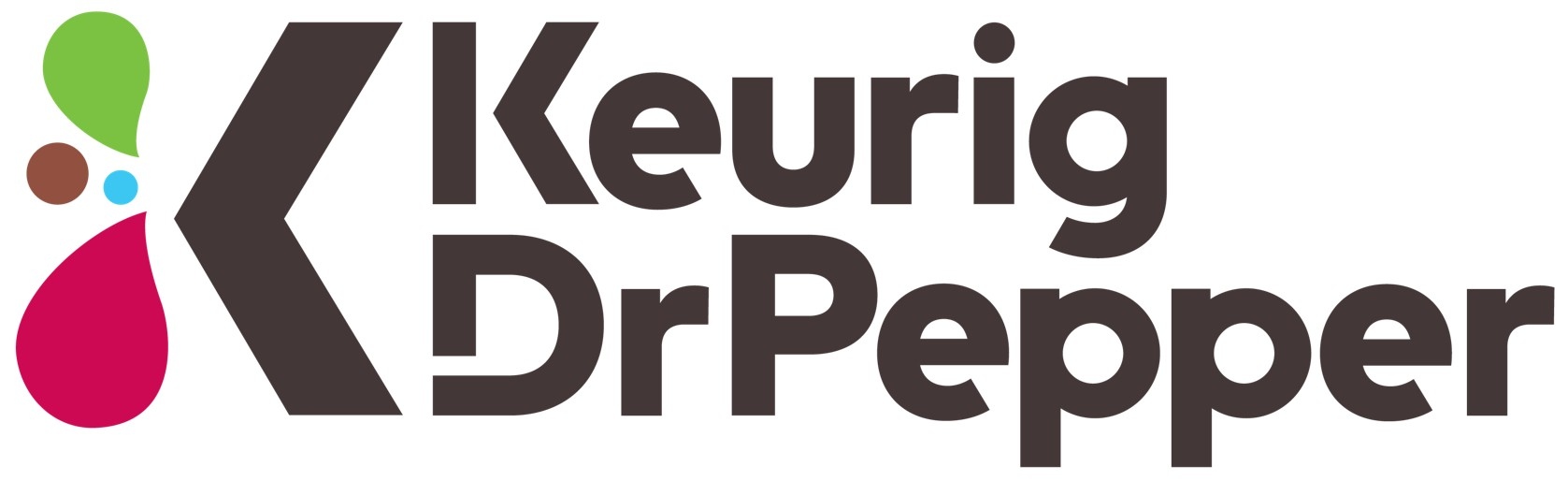
Designing for single parcel distribution poses many challenges associated with cost, material limitation, aesthetic tradeoffs, and multi-channel compatibility. With the recent update to Amazon's SIOC program, many CPGs are having to confront these challenges to avoid chargebacks and ultimately practice 'responsible packaging by design.' As an early adopter of the SIOC program, Keurig Dr Pepper has implemented numerous packaging changes to enable SIOC compliance and an omni-channel focused packaging portfolio. Having cycled through this program several times, we'd like to share key learnings and best practices for the major phases of the certification process; eligibility assessment, test execution, and enrollment.
Takeaways: This presentation is aimed at sharing KDP's day-to-day interaction with Amazon's SIOC certification process. Ground-level perspective and lessons learned will be highlighted by real-world examples. This is meant to be thought-provoking and help you tailor your organization's approach when participating in the program.
Kara Revoir Biography: Education: BS Biological Engineering, Cornell University, 2010. Kara spent her early professional career as a Process Development Engineer and has recently moved into Packaging Engineering. She is focused on packaging performance across KDP's many distribution channels and is responsible for major network-wide productivity initiatives. ISTA CPLP Technologist.
Lucas Magnant Biography: Education: BS Packaging Engineering, Rochester Institute of Technology, 2011. Luke currently works at Keurig Dr Pepper as the Packaging Engineering Manager responsible for secondary/tertiary packaging and management of KDP's ISTA-certified dynamics lab. ISTA CPLP Technologist.
Influence of Fiberboard Container Design on its Bulging Performance Impacted by Compression

Student
California Polytechnic State University

Student
California Polytechnic State University
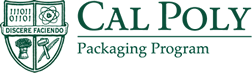
Corrugated container bulging impacts the packaging industry by affecting pallet load destabilization, compromising container strength, and vibration damage. Bulging changes the geometric shape of the container, causing the palletized load to take up more space than anticipated. This causes the stretch wrap to contact other surfaces during transit which leads to tears and further unit load destabilization. The purpose of this study is to identify a relationship between bulging and container design elements such as styles and dimensions. The findings of this study will assist packaging engineers to reduce material usage, maximize container stacking strength and rigidity. The study is intended to showcase the significance of quantifying container bulge towards developing optimum distribution packages.
Takeaways: Packaging engineers will have a way to quantify and predict package bulging. The methodology can be used to assist the industry in selecting optimum corrugated fiberboard containers towards minimizing undesirable bulging related issues in distribution related activities.
Shane Messner Biography: Shane Messner is currently in his final year as an undergraduate student in the Industrial Technology and Packaging program at Cal Poly University. His interests include packaging testing for optimal protective packaging design and packaging sustainability. In 2019, Shane worked on a research project for Cal Poly to understand the impact of corrugated container design and environmental conditions on its bulging performance in distribution.
Marilyn Nguyen Biography: Marilyn is in her senior year as an Industrial Technology and Packaging undergrad student at Cal Poly. Within the world of packaging, she is especially interested in innovative package designs that not only protect the product but also provide a unique experience for the consumer. Marilyn has worked at Applied Medical in Rancho Santa Margarita, CA as an packaging intern, helping optimize the manufacturing process for laparoscopic medical devices.
ISTA Advocate Research & Value Delivery Program Update

Advocate Program Manager
ISTA
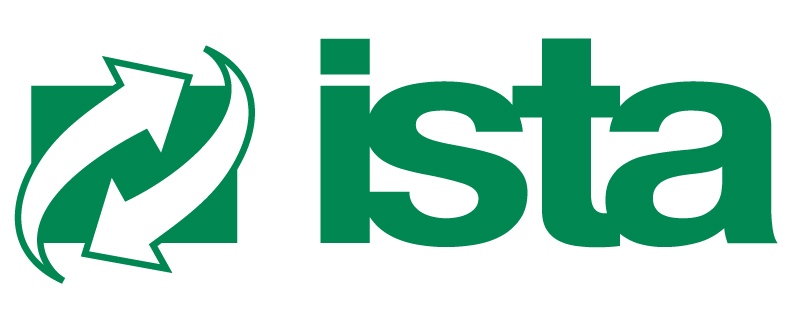
Biography: Dwight Schmidt is President of Consult Schmidt, LLC a consultancy focused on providing its clients with strategic direction, improving operational rigor and developing sustainable organizations. He also consults in the area of non-profit association operations and mergers and acquisitions in the packaging space. He served as the Executive Director of the Corrugated Packaging Alliance (CPA), from 2002 – 2012. He was President of the Fibre Box Association (FBA), a trade association representing more than 90 percent of U.S. converted corrugated from 2006 -2011. From 2007 - 2011, he was the International Corrugated Case Association’s (ICCA) Vice President of the Americas. Education: Graduate of Michigan State University’s School of Packaging and holds a Master of Business Administration from the University of Evansville and has completed the Executive Program at the University of Virginia’s Darden School of Business. Activities: Board member and past chairman of the International Corrugated Packaging Foundation (ICPF), long-standing board member of the International Safe Transit Association, long-standing member of the Michigan State University, School of Packaging, Industry Advisory Board and a former board member and President of MSU School of Packaging Alumni Association. As a participant in packaging industry activities he is, or has been, a member of the Institute of Packaging Professionals (IOPP), the American Society of Association Executives (ASAE), the Technical Association of the Pulp and Paper Industry (TAPPI) and a board member of the International Safe Transit Association (ISTA). He also has served on the Industry Advisory Board of Virginia Tech’s School of Unit Load Design, the Paper Industry Advisory Council (PIAC), and Wal-Mart’s Packaging Sustainable Value Network. In addition, he has held numerous offices and committee appointments within his professional organizations. Achievements: Induction into the PMMI Packaging Hall of Fame. A patent holder and published, he has been a speaker at numerous regional, national and international corrugated and packaging industry forums and seminars in the U.S. as well as Australia, Canada, the Czech Republic, Costa Rica, Ecuador, Ireland, Italy, Japan, the Netherlands and Sweden. He has been recognized by his fellow packaging graduates by being elected to their Hall of Fame in 2000, and in 2002 he received Michigan State University's “Distinguished Alumni” award.
Distribution Environment Data Collection Project, India: CPGs and Small Parcel

Professor & Director
California Polytechnic State University, San Luis Obispo
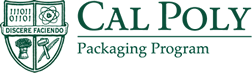

Instruments Product Manager
Lansmont Corporation
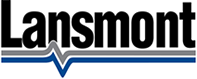
From the perspective of eventually developing representative pre-shipment test protocols, this ISTA supported study undertook an extensive instrumented evaluation of (1) the land routes associated with the movement of CPGs within, near and between the Jawaharlal Nehru Port (Mumbai) and New Delhi, and (2) small parcel shipments between four major cities in India. 39 instrumented trials spanning over 11,600 kilometers of land routes for the distribution of CPGs associated with six major companies were included in the study. The small parcel trials involved 36 instrumented shipments using two major couriers over approximately 10,000 kilometers of distribution activities. This presentation summarizes the distribution environment data collected for the distribution of CPGs and small parcel shipments.
Takeaways: Primarily due to economic growth, increasing participation from foreign and private players, policy support, innovation in financing and an astounding online retail growth, the Indian retail industry is one of the fastest growing markets in the world. This presentation avails the attendees with an opportunity to understand distribution activities unique to India. The outcome of this study is aimed at developing currently outdated/limited pre-shipment test protocols for distribution practices specific to India.
Jay Singh Biography: Jay received his MS and PhD in Packaging Science from Michigan State University. Considered amongst the top experts in the field of distribution packaging globally, Jay has published over 95 peer-reviewed articles, 73 articles in conference proceedings, 32 trade journal articles, 3 book chapters, coauthored 2 books and edited 1 book. A number of his publications have resulted in development/modification of numerous globally acknowledged packaging test standards. Jay currently serves as the President of International Association of Packaging Research Institutes (IAPRI) and is a past Director on International Safe Transit Association’s (ISTA) Global Board. Having undertaken funded research of over $5.3+ million from state, federal agencies and industry as well as currently holding four patents, Jay was recognized with the Distinguished Scholarship Award in 2017 by Cal Poly. Jay is also the recipient of the ISTA 2019 R. David LeButt Award.
Grand Badstubner Biography: Grant Badstubner holds an MS in Packaging Value Chain and a BS in Industrial Technology from Cal Poly SLO. He is currently the Product Manager for the SAVER and Test Partner product lines at Lansmont Corporation in Monterey, California. In his 3 years at Lansmont Corporation, Grant has participated in half a dozen distribution measurement projects for a variety of companies in the CPG and medical industries. His hands-on experience with field data collection and analysis empowers customers to make data-driven decisions based on real-world dynamics. When he isn’t busy with work or school, Grant enjoys travel, scuba diving, and golf.
Understanding Constructed Probability

Senior Engineer - Global Packaging
Eli Lilly & Company
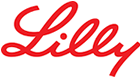
In recent years Eli Lilly has increasingly relied on simulation of vibration during product development to reduce the risk of damage during product transportation. Currently, our approach is to use both compressed and uncompressed vibration profiles to ensure that the product is robust to vibration of both high amplitude and long duration. As biological drug molecules become more complex and more varied, we are beginning to encounter products for which compressed vibration testing can predict damage that is not observed during over the road shipping studies and uncompressed vibration testing based on average PSDs can fail to predict damage that is observed during over the road shipping studies.
This creates a need for more precise simulation tools. We need vibration profiles that combine accurate high, medium and low stress levels in realistic proportions in a single test with a worst-case transportation timeline. The multi-level profiles provided in ASTM 4169-16 are a step in this direction, but they are based on the standard steel spring truck model, and we need to have both steel spring and air ride models as well as models for air and rail transport. Furthermore, we would like to base these models on our own specific shipping lanes.
Lilly has developed profiles that adjust the vibration level to the 95th percentile and compensate for kurtosis to the extent possible using academically recognized methods, but these profiles apply the same compensation factor at each frequency and apply the same profile for the entire simulation.
As a result, these profiles still miss the peak values above 95% and badly overtest the mid-level values between 50 and 95%.
In addition, the kurtosis calculation is somewhat complex and subject to debate, and the 95th percentile PSD is based on a group of average PSDs, not on the fundamental vibration data.
Takeaways: This presentation will seek to explain what is meant by 'Constructed Probability' and how it can be applied to vibration testing of transportation systems.The engineering context in terms of needs and issues surrounding monitoring and simulation of vibration and shock during distribution of commercial products will be reviewed, with emphasis on opportunities for improvement.
Biography: I grew up in the San Francisco Bay Area and earned a BS in Engineering from Boston University and an MS in Engineering from MIT. Prior to joining Eli Lilly in 2003, I worked as a navigation systems engineer for Northrup, in product development and sales for a spin-off from Woods Hole Oceanographic, in development of mobile inspection robots for hazardous environments at Raytheon and, for a short time, as a program manager at Enron, responsible for quality assurance for the Lilly contract. At Lilly I have supported Facilities Delivery, Device Development, Serialization and Packaging Engineering. For the past two years I have been leading the vibration testing program.
Load Stability Simulation of Horizontal Accelerations at the Laboratory Versus Real Events

CEO
Safe Load Testing Technologies
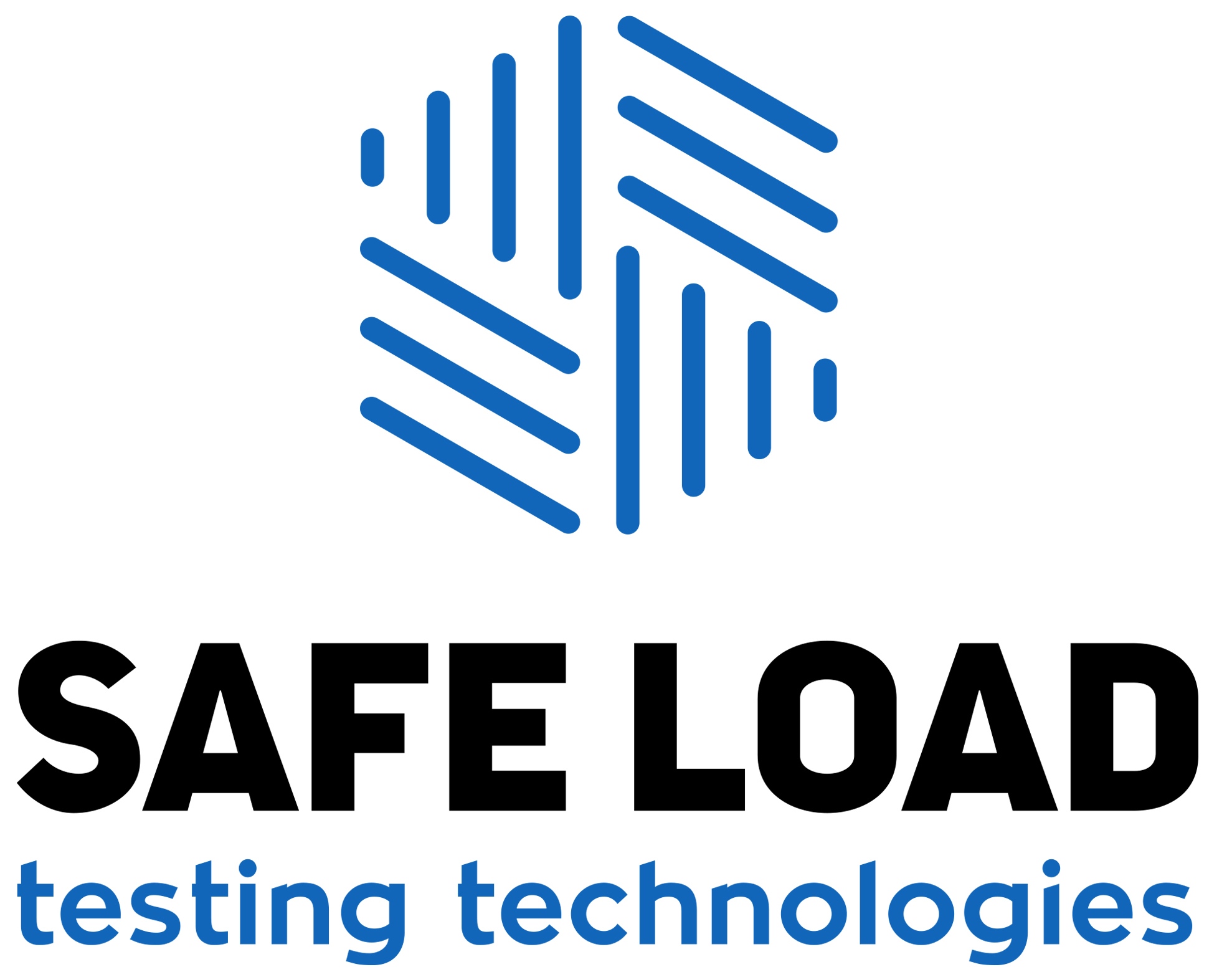
Regarding the increasing interest of transport authorities and the scientist community about the load stability during transportation and its right simulation at laboratory, several works have been done and published. One of the theoretical studies presented at IAPRI 2019, with the title 'Emergency braking and Stability testing, Response Analysis' showed why the horizontal natural frequency of the unit load it is determinant for the response level of the unit load subjected to that acceleration curve. In that study was demonstrated that a maximum of 200 ms time jerk duration to get the steady acceleration following by a minimum of 300ms time dwell duration of a trapezoidal pulse it is required to get exactly the same response as produced in a real emergency braking for unit loads of horizontal natural frequency greater than 1,2 Hz. Because It's hard to understand how a test shortest than 1s can simulate the effect of a real braking of the same intensity which can hold several seconds, we have undertaken a new practical study using a real unit load inside a vehicle. This unit load has been monitored with high speed cameras and other devices to measure the real deformation and accelerations that this unit load is going to reach during the transportation acceleration events. This deformation has been compared with the deformation produced on the unit load simulating the real acceleration event with different dwell durations in the laboratory using a horizontal stability machine, in order to visualize the low deviation that we obtain from real world versus simulation in the laboratory.
Biography: Alberto Tellechea is the CEO of Safe Load Testing Technologies, an international supplier of transport simulation solutions for packaging optimization and validation. He is Industrial Engineer by Polytechnic University of Valencia, major in Management and holds an MBA from the School of Industrial Organization of Madrid. Alberto counts with more than 10 years of experience in General Management of companies belonging to several industrial sectors such as machinery, ceramics, plastic engineering and the transfer of industrial fluids. Currently Alberto is member board of EUMOS and collaborates in working groups of the most important committees in the packaging testing field: IAPRI, ISTA, EUMOS.
Your Front Porch | If it can make it there, It can make it anywhere: The Untold Story of an e-commerce Package

Packaging Product Test Engineer
Bureau Veritas
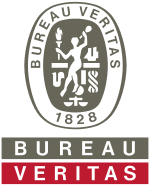
The presentation will explore the world of ecommerce distribution. There will be firsthand experience shared, demonstrating the new hazards this form of distribution has created. This will be contrasted against traditional shipping environments, in hopes to demonstrate a new approach to package design and testing evaluations may now be a necessity.
Takeaways: Attendees should be able to form a connection between laboratory test simulations and how they relate to the real world. They should be able to take away at least a few examples of potential real world hazards they may have overlooked when analyzing individually packaged product distribution networks. It will provide insight they can apply to their own distribution simulation strategies.
The goal is to remove preconceived notions about the world of ecommerce distribution based on data and experiences from traditional warehousing and shipping networks.
Biography: Anthony is a graduate of Packaging Science program at The Rochester Institute of Technology. He has been working in the shipping and packaging industry for the over 10 years and is a CPLP Technologist. He currently leads the Amazon ISTA-6 testing team at Bureau Veritas and is focused on innovations for growing world of e-commerce distribution testing.
Tackling Damage of Fragile Products: The Home Depot’s Journey to Driving Packaging Improvements

Packaging Consultant, Packaging Engineer
Chainalytics
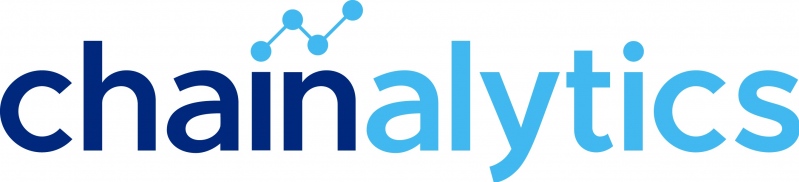

Packaging Engineer
The Home Depot
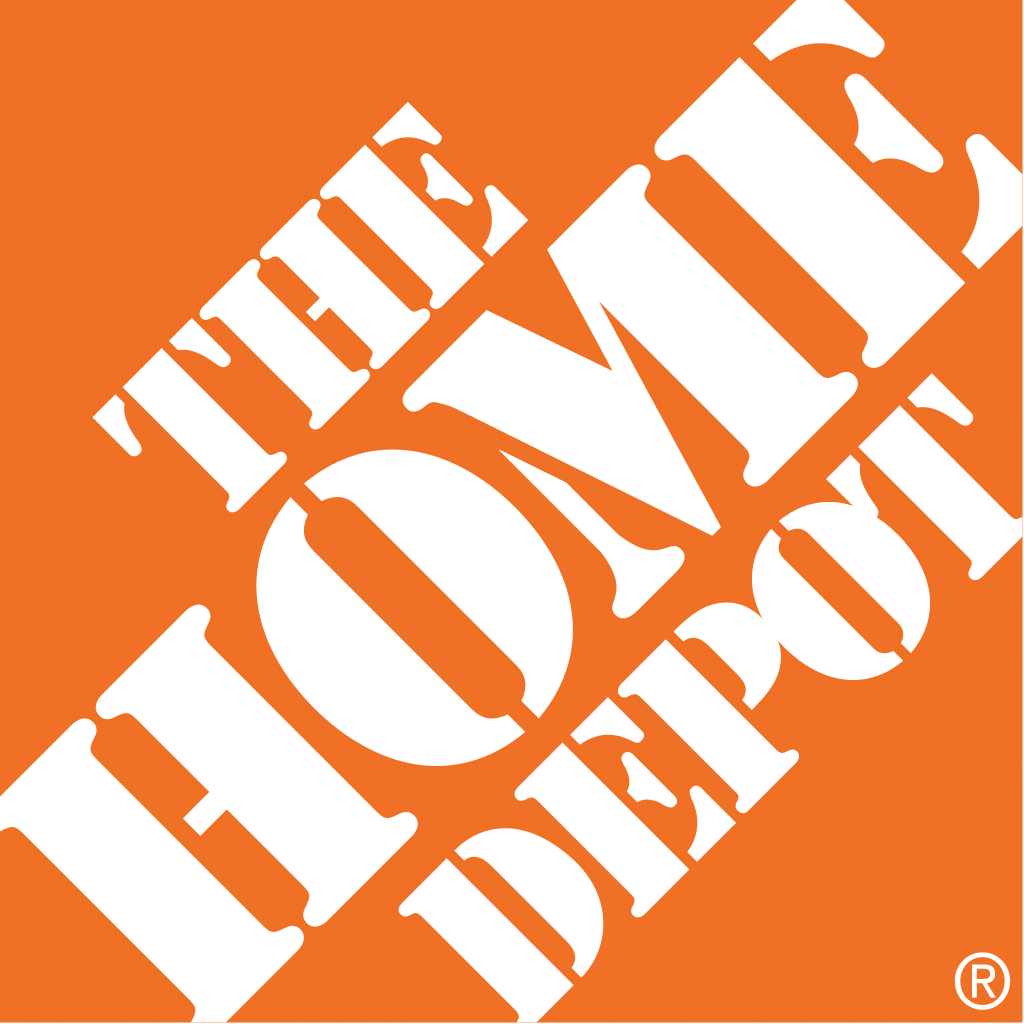
From 2017 to 2018, The Home Depot – the world’s largest home improvement retailer with more than 2,200 stores in North America and over 1 million products available in its physical and online stores – experienced significant damage costs from in-store markdowns and customer returns across three of its tile product subclasses – all of which were coming from a single manufacturer. Recognizing the need to drive tangible change and execute improvements within a cross-functional team, The Home Depot partnered with Chainalytics to gain a better understanding of its end-to-end supply chain hazards as well as develop effective packaging solutions and packaging design guidelines.
In this session, The Home Depot will explain how they tackled the extraordinary damage rates and costs within this fragile product category, why they chose to leverage an external partner for the supply chain assessment and solution development phases, and what value has been created by the recommended packaging and process changes.
Takeaways:
- A practical approach for identifying the root cause(s) of product damage
- Greater appreciation for the value of an end-to-end supply chain mindset as well as understanding challenges introduced by inherent product characteristics
- Tips for enacting tangible change with contract manufacturers and suppliers
Alex's Biography: Alex is a Consultant in the Packaging Optimization practice at Chainalytics. In this role, he provides end-to-end engineering support for packaging optimization projects, working to ensure solutions improve costs, improve packaging performance, and consider environmental impacts. Education: Michigan State University 2017 - B.S. Packaging. Job Title: Packaging Consultant, Packaging Engineer at Chainalytics. Professional Achievements: CPIT (Certified Packaging Professional in Training), CAPM (Certified Associate in Project Management). Industry Experience: Electronics, Consumer Products, Medical, Retail, Industrial, Large Appliances.
Eileen's Biography: Eileen graduated with a bachelors degree in Packaging Science from Michigan State University in 2017. Currently, Eileen is a packaging engineer for the Global Brand & Product Development team at The Home Depot, specifically focusing on hard and soft surface flooring and packaging sustainability.
Closing the 72% Percent Gap: Perceived (Theoretical) Customer Packaging Experience vs. Actual Customer Packaging Experience

CEO
The Design Doc Enterprises
“Today, 89% of companies compete primarily on the basis of customer experience – up from just 36% in 2010. But while 80% of companies believe they deliver “super experiences,” only 8% of customers agree. In other words, companies have a long way to go. And, that means there is tremendous opportunity to disrupt a competitor or gain market share in an industry. Everything a brand does – the way it does its marketing, research, advertising and more – all play a role in shaping the customer’s experience.”
When packaging is purchased especially from the manufacturer the focus is to protect, and preserve is the paramount consideration. Based on theory, the packaging SHOULD open and operate as designed. Countless number of packaging is produced, shipped, and placed on store shelves WITHOUT a thought of “does this packaging work the way we said it should?” What does the customer experience when they interact with your product packaging? The customer must be considered in the packaging development process. Customers must have a permanent role in the packaging process. Customer packaging experience testing is essential to closing the gap between perceived customer packaging experience and actual customer packaging experience. A positive customer experience is the new “bottom line” and creates revenue.
Takeaways:
- Understand the power of customer experience and packaging
- Positive consumer experience creates revenue
- Positive consumer experience builds and maintains loyal customers
- Customer packaging experience testing methods
Biography: Vickie L. VanHurley, Ph.D. is presently an educator, entrepreneur, artist, author, founder & owner of Design Doc Enterprises, LLC. She is a branding expert and the entrepreneur’s branding educator. Vickie is sharing her love of branding, brand packaging design, and customer experience through packaging with students as an adjunct professor at the University of Tampa and Florida Southern College, Department of Communication and Department of Art and Design. She is also sharing her passion for branding with business owners and startups with her book Bootstrap Branding: An Entrepreneur’s Guide to Building a Brand with Limited Finances. Vickie is helping business owners brand from the start. She also is a consultant with a “hands on” approach helping build brands via brand packaging. Vickie also shares her passion for branding through packaging as a conference speaker, author, blogger, and podcaster. Prior to becoming an entrepreneur Vickie was packaging design director for Meijer, a major mid-western mass merchandise retailer from 2007 to 2011 in Grand Rapids, MI. Prior to her position at Meijer she was an instructor of advertising layout & design at Michigan State University in East Lansing, MI from 2004 to 2007. Prior to arriving at Michigan State University Vickie was an assistant professor and Program Director of Graphic Design in the College of Fine Arts at the University of Kentucky in Lexington, KY from 1998 to 2000. Vickie was also an instructor in the Department of Commercial Graphics-Design in the College of Technical Careers at Southern Illinois University-Carbondale, Carbondale, IL from 1994 to 1998. Vickie previously taught courses in the Department of Advertising and School of Journalism before her full-time appointment at Michigan State University where she earned her Ph.D. in Mass Media with a packaging design and advertising design emphasis in 2007. Vickie has always been a patron and participant of the arts. She has been a graphic designer and illustrator for over 30 years, which includes over 10 years of corporate design. Vickie is also an accomplished illustrator with art displayed at The Flint Institute of Arts, the University of Kentucky, Osceola Center for the Arts, National Art Education Association, and Modern Museum Art Magazine. Vickie has been cultivating the artistic talent of others for more than 25 years. More specifically, she has been a college professor for 17 years.
Testing Naked - The Benefits of Testing Unit Load Stability without Unit Load Packaging

Packaging Engineer
Highlight Industries
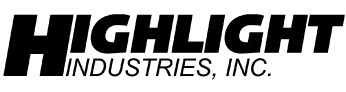
Unit load stability testing projects typically begin with a fully packaged pallet or shipping container. These loads are tested for stability and the packaging is adjusted until an acceptable result is reached. This presentation shares the lessons that Highlight Industries has learned by starting unit load stability projects by FIRST running transportation simulations WITHOUT using any stabilizing packaging (stretch film, strapping, etc.). By testing product stability in an unsupported and unprotected state, raw data can be collected which gives valuable insight into what the stabilizing packaging really needs to do in order to protect the package during transportation.
Takeaways:
- What does your stabilizing packaging (stretch film, strapping, etc.) really DO?
- What is a unit load's "natural stability" and why does it matter?
- The physics and mechanics of how stretch film stabilizes unit loads.
- How and why do unit loads fail, and how can understanding that lead to using less packaging.
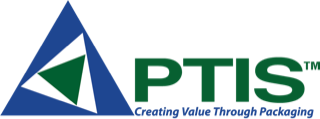
Since 1997, PTIS and Leading Futurists have led year-long programs with dozens of leading companies from across the Packaging value chain – the most recent, completed in 2019, The Future of Packaging 2030. The program looks out 10 years and helps companies use foresight to plan for the future. A crucial program input is a global thought leader survey. 146 Respondents included experts from leading companies, academia, and respected leaders in the packaging and related areas. The survey goal is to gain a perspective of key impacts, technologies and trends that will influence packaging by 2030.
Takeaways:
Global Thought Leader survey results:
- Prepare to focus on what matters
- Eliminate what doesn’t matters
- Live intentionally every day
Biography: Brian Wagner’s 30-year professional career as an entrepreneurial business and technical leader spans PTIS, HAVI, Kellogg's, Sara Lee, Multiform Desiccants, Carton- Craft Corp., Burger King and General Foods. He served as Ameripen Director, 2017 and 2018. In 2008, he was inducted into the Michigan State University School of Packaging Hall of Fame and was recognized as 2008 Western Michigan Business Review – Thought Leaders. In 2016, Brian received the Reister-Davis- Brody Lifetime Achievement in Food Packaging, and the R. David LeButt Packaging Education award. He is an Executive in Residence at the WP Carey Business School at Arizona State University, and advisor to Cal Poly’s Packaging program. He has contributed to numerous industry journals and publications, including the 2012 book, Creating Value Through Packaging. He earned a Bachelor of Science degree in Packaging from Michigan State University.
Representative Shipping Through Distribution Testing

Packaging Engineer
Merck & Co.
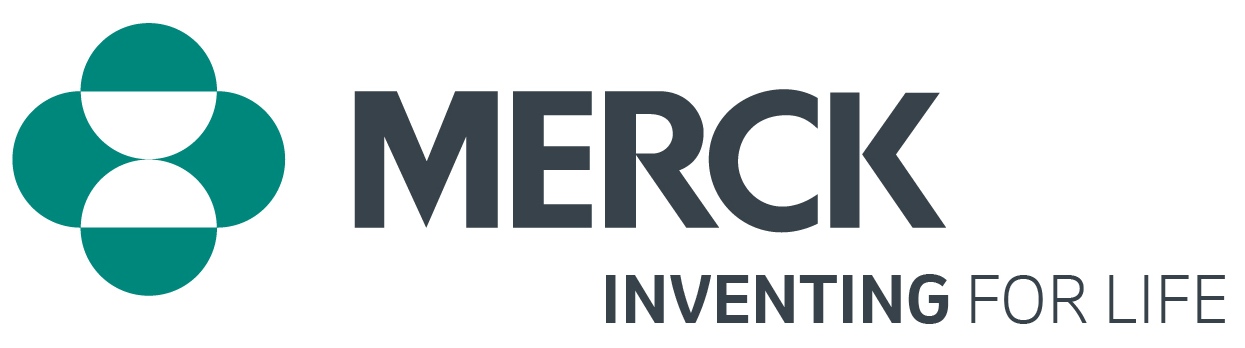
In 2011, Merck created a distribution test series for parcels using lane-specific data in North America and when the ISTA 3A series was placed on the recognized consensus standards list, Merck performed a comparison of that parcel test to the ISTA 3A and its equivalency. This presentation looks to compare a general series 3A parcel test to real world data and explore how distribution testing in a lab truly reflects what a parcel may experience in actual distribution.
Additionally, how can known hazards and forces in distribution help reduce the amount of testing needed on a wide range of product images? Is it possible to test in one outer container to cover shipments in other similar containers? This discussion involves using real world data, cushion curves, and impact forces of individual cushions and complex systems to pose a new approach to distribution testing using the existing test series. Using accelerometers, Lansmont SAVERs, and new SmartSkin Drone technology to gather this data and create representative results of distribution tests, we hope to provide examples and lessons learned from this style of testing and welcome discussion on how to improve this method of qualifying images for shipment.
Takeaways: The key takeaways of this discussion are to give real-world examples that support the general series test that is the ISTA 3A, to highlight the method of approach Merck uses the ISTA parcel tests for and pose some suggestions on how to improve parcel testing with existing test methods and technology now available in industry.
Biography: Education: Graduated Rochester Institute of Technology with a BS in Packaging Science and has been working at Merck for three years in Logistics and Distribution Technology. Her focus at Merck is distribution testing practices and supporting cold chain packaging globally by qualifying thermal protection systems, as well as being involved with Child Resistance / Senior Friendly packaging. Matilda is part of the Merck Diversity and Inclusion team.